A medieval blacksmith, including a woman artisan, from ‘The Romance of Alexander’, c. 1340 CE. (via the Bodleian Library)
The emergence of blast furnacing in 13th century Medieval Europe heralded the medieval steel revolution. Before, steel was made on a small scale, by individual artisans with the help of a handful of apprentices using basic tools and simple clay chimneys. Within a century, it was being made in something that much more closely resembles the modern industrial steel foundry: towering blast furnaces many storeys high, powered machinery that never stopped, and teams of workers toiling around the clock.
Iron, Steel and Medieval Metalwork
What are the differences between iron and steel? Iron is a dull-grey metallic element, and when pure it is reasonably soft and, on its own, not all that useful. It doesn’t hold an effective edge for tools or weaponry, and can be bent fairly easily. Steel is an alloy (metallic mixture) of iron and another element: carbon. It is much harder, and extremely useful, since it holds an edge and, if properly treated, is slightly elastic, being able to spring back into shape when impacted. This makes it fantastic for the edges of tools, weaponry and armor. High-carbon steel (0.3-1.7% by weight), for example, was laborious to make, but was perfect for performance applications like the edges of weapons. Low-carbon steel (0.05-0.3% by weight) was excellent for the ploughshares and scythes, for example.
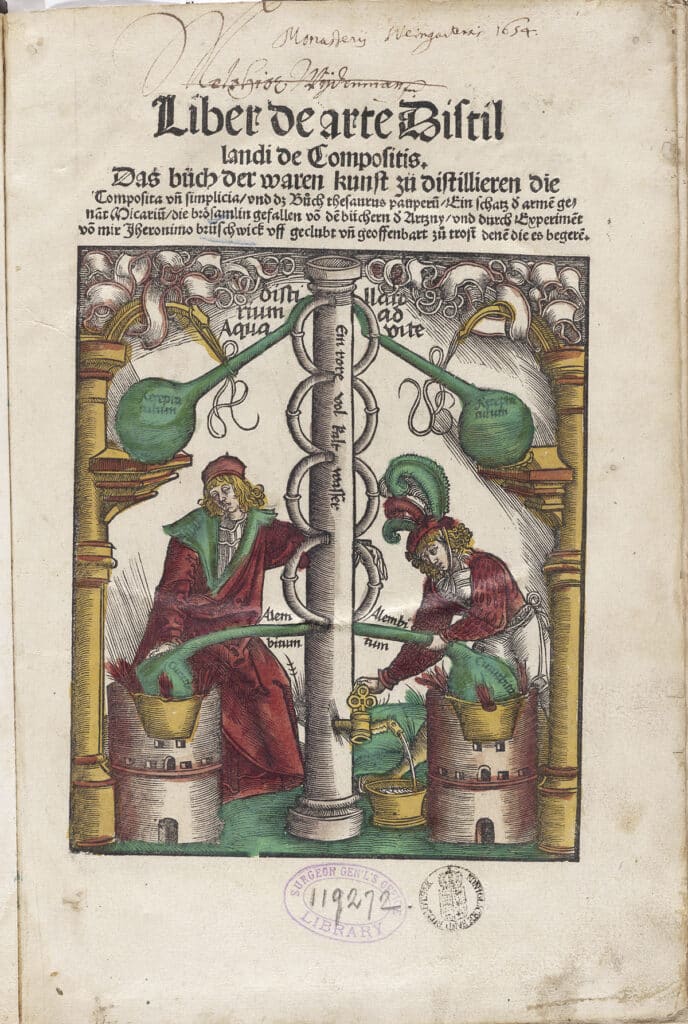
Although even the best medieval scientists had no concept of chemistry in these terms, medieval metallurgy was largely about controlling the amount of carbon in the iron-carbon alloy to create things for specific purposes – there was no ‘ideal’ steel that would do all jobs. It is an enormous testament to the skills of the medieval metalworker that such works of craft were refined by trial, error and ingenuity between master and apprentice over the course of centuries.
Let A Thousand Iron Flowers Bloom
Ever since ancient times, the primary way of making iron and steel was the bloomery furnace. This method involves creating a conical ‘chimney’ from clay, usually between three and six feet in height, filling it with a mixture of charcoal and crushed iron ore, lighting it at the bottom, and fanning it constantly with either one or two pairs of hand-bellows. Bloomeries could generally achieve heats up to a maximum of c. 1,000ºC / 1,800ºF – hot enough to cause a ‘reduction reaction’, where the oxygen is removed from the iron oxide in the ore, leaving behind a mass of solid iron and slag called a ‘bloom’. This would then be further refined by heating it up and hammered the slag out of it, producing reasonably pure iron. For more on this process, see ‘How Did Medieval People Make Steel?’.
Bloomery Steel and Carburization
Experimental archaeology (ie. trying out historical methods in the real world) has demonstrated that you can actually make steel straight from a bloomery, by using a high proportion of charcoal and, paradoxically, ensuring the bloomery doesn’t get too hot – this results in carbon being distributed throughout the iron, creating a carbon-steel alloy.
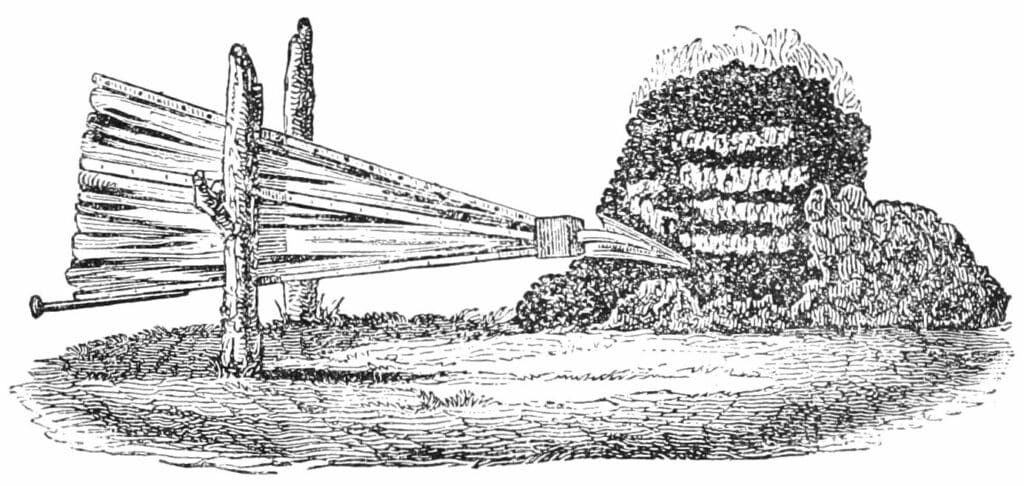
But this was an extremely skilled and often haphazard task – most bloomery iron was very low in carbon. Hence, to make steel, it had to be ‘carburized’, ie. alloyed with added carbon in order to make the desired hardness of steel. This could be done in several ways: a suit of chainmail might be made from iron rings, then rolled in charcoal dust and baked in a clay casket to ‘case-harden’ it, the carbon diffusing into the surface of iron. Alternatively, rods of bloomery iron could be hot-worked by a smith or their apprentices in a charcoal-fired forge over and over, gradually increasing the proportion of carbon in the rod. This was extremely labor-intensive, and only ever resulted in small amounts of steel.
Put On Blast
The blast-furnace changed this entire process. Starting around the middle of the 13th century, a qualitative change in iron production took place. Bloomeries had gotten larger and larger throughout the High Medieval era as the population had grown, warfare and the economy had scaled up, and demand for iron increased. Large bloomeries are exponentially more efficient, are are able to reach much higher temperatures. The real revolution came with the application of water power to these large bloomeries. By scaling up the bellows and powering them with a water wheel, furnaces could be supplied with a constant ‘blast’ of air that was capable of generating enormous heat.
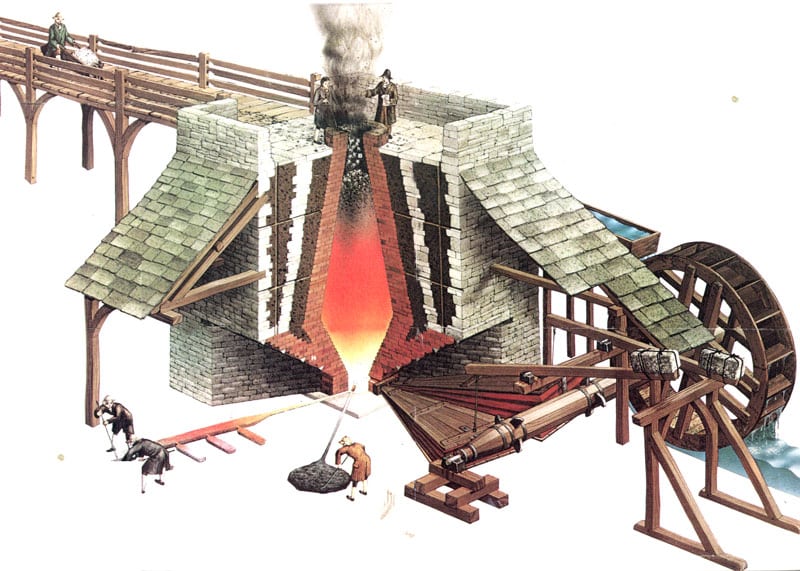
This method of water-powered iron production was widespread in China from the 1st century CE, but there is some debate as to where and when this process started in Europe. Some of the earliest are at Nya Lapphyttan, central Sweden, dating to somewhere between 1150 CE and 1350 CE – historians theorize that Chinese blast furnacing techniques spread along the Silk Road, and up the Volga trade routes into Scandinavia. By the 15th century, blast furnacing had become common across Europe, with centres of iron production in northern England, western France, Switzerland and Sweden.
Cast Iron, Pig Iron and the Finery Forge
Now, ironworkers could achieve temperatures hot enough to blow way past the melting point of iron (1,538ºC / 2,800ºF). This meant that, instead of a solid reduced-iron bloom, liquid iron would run from the bottom of the blast furnace, which could be poured into casts, creating the first cast iron. This cast iron (known in raw form as ‘pig iron’) was generally much purer than bloomery iron, its liquid state permitting slag to be simply skimmed off the top – but it contained far more carbon than even high carbon steel (usually more than 3% by weight). Whilst this brittle, extremely hard iron kickstarted the casting of cannon, it was not useful for tools, weaponry and armor.
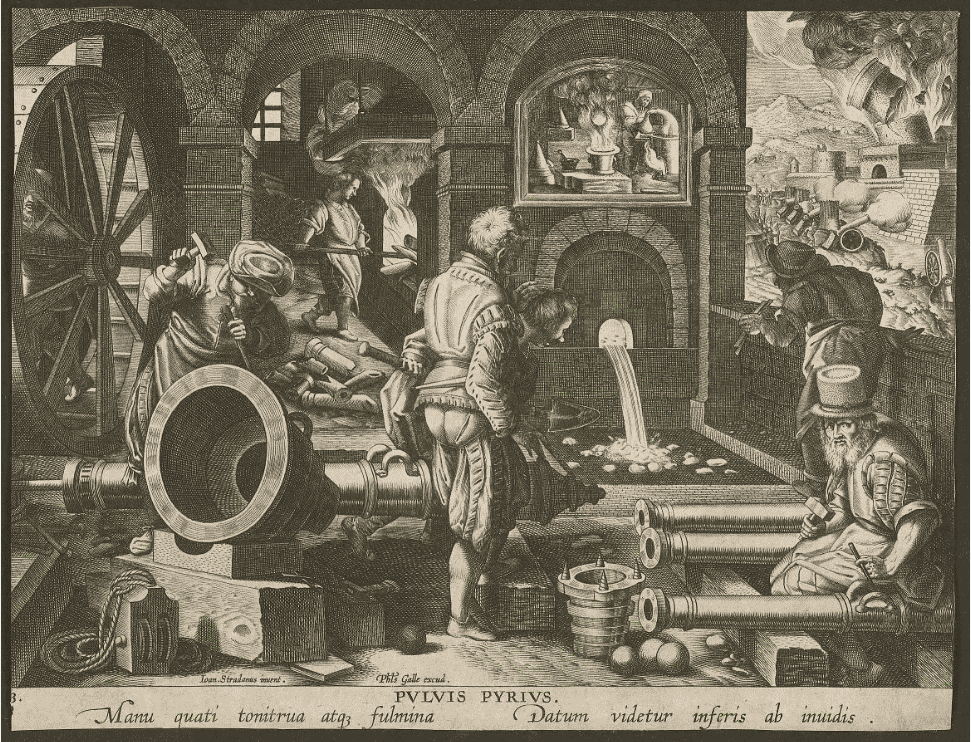
Hence, rather than starting from near-pure bloomery iron and carburizing it into steel, now you would start with large quantities of high-carbon pig iron which would need to be decarburized. This gave rise to a whole new series of industrial processes: finery forges, osmond hearths, and others resulted in a much greater division of labour.
The Pre-Industrial Revolution
The Late Medieval steel revolution boosted steel production exponentially, and created industrial environments which (although on a far smaller scale) are much closer to those seen at the dawn of the Industrial Revolution three centuries later. It was this fundamental shift from artisanal to industrial production which created the material basis for knights in shining plate armor, and the grand-scale conflicts of the Late Middle Ages.