So – you’ve watched all 9 seasons (235 episodes!) of History Channel’s Forged In Fire. You know everything you need to forge your own Damascus blades and become a master bladesmith. Right? If it was that easy, then everyone would be a master swordsmaker! Don’t get us wrong, Forged In Fire is a great TV show, but it’s definitely an entertainment show rather than a realistic depiction of the craft of blacksmithing. Real mastery of bladesmithing is a lifelong craft. That said, the enormously increased profile of historical metalworking – due in no small part to Forged In Fire – has means that the barriers to learning bladesmithing are lower than ever. Blacksmithing books, blacksmithing YouTube videos, blacksmithing courses and even blacksmithing university qualifications abound to get you started on how to become a bladesmith. In this article, we’ll give you a few simple ways to get into the craft of blacksmithing – so you can begin your journey toward becoming a master bladesmith.
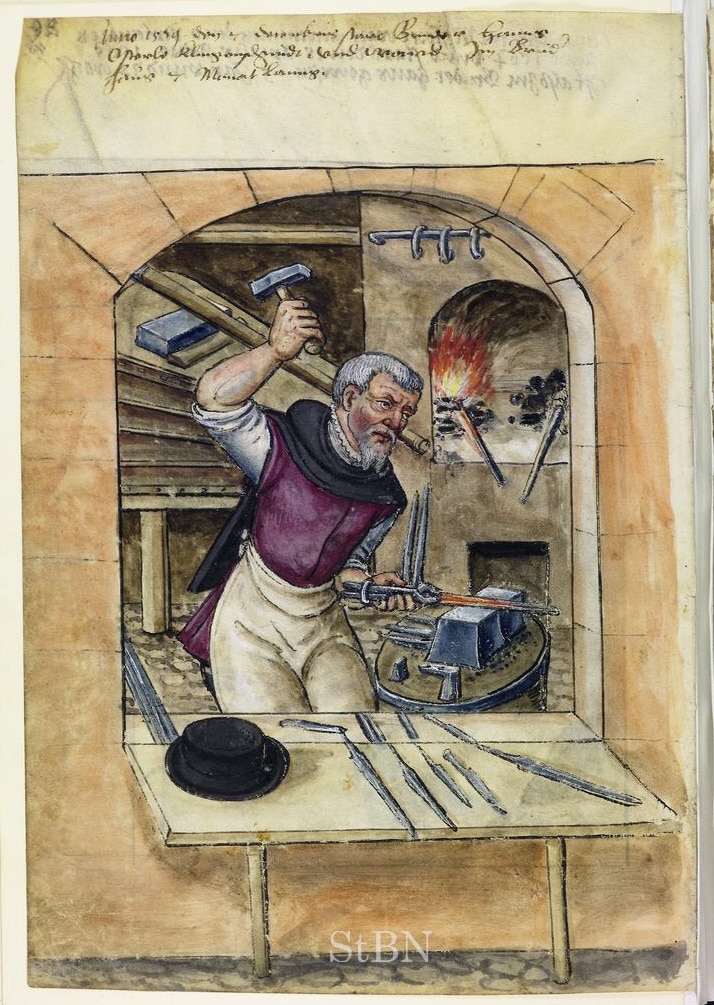
Try It Out
Our number one starting point for how to become a bladesmith is: go give it a try! Blacksmithing is undergoing a renaissance as a heritage craft, with many blacksmiths set up across the Western world. And many of them make at least part of their living by teaching the craft to enthusiastic amateurs who want to try their hand. A great place to start is going for a day course to get a taste for what historical metalwork involves.
Blacksmithing taster courses are often built around making one simple object – but don’t let the simplicity fool you! A common item to make is a fire poker, with a point for stoking, a twist in the center of the haft, and a hook that doubles as a grip and a means of hanging it when not in use. Starting from a length of ½ inch square mild steel stock, this simple project requires the use of all four of the basic techniques of blacksmithing: forging, forming, twisting and cutting. First, you will forge the point into the end of the poker, then you will cut lines into the length of the stock with a hot chisel, then you will apply an even heat to the center of the stock and apply a twist, and finally, you’ll form the hook/grip over the horn of the anvil. Even knowledgable blacksmiths always have more to learn (I’m a budding blacksmith and I went on a day course a few weeks ago, and I got masses out of even re-learning the basics!).
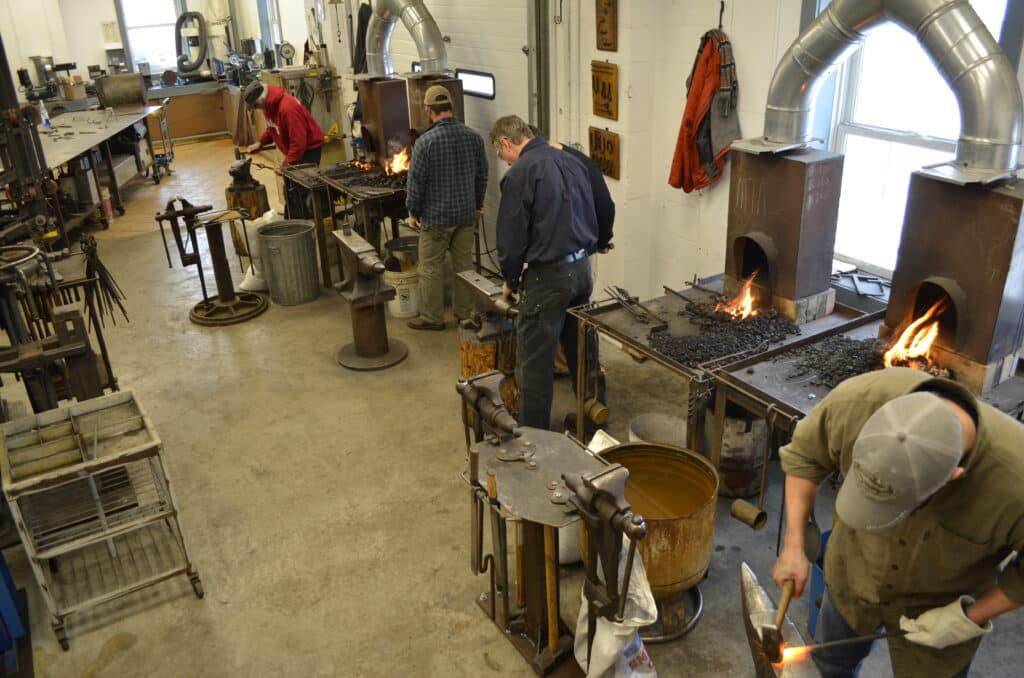
It may seem like a waste of time – of course you want to learn bladesmithing – but it’s better to come away from a day course enthused and raring to go, than it is to spend all your savings on a home forge setup and then discover that it’s not for you! Blacksmithing day courses are widely available in every US state and most countries. Contrary to stereotypes, blacksmiths tend to be pretty good at living in the 21st century, and so many courses and experience days are easily discoverable on the internet.
The DIY Route: Teaching Yourself
Historically, metalwork was a closely-regulated trade, with secretive guilds that tightly controlled the transmission of knowledge from master to apprentice. Nowadays, we have YouTube. Obviously that’s somewhat of an exaggeration – the gradual change from private, guild-regulated knowledge toward publically available knowledge and mass education was one of the results of the Industrial Revolution in North-Western Europe, with trade guilds gradually replaced by trade unions which had much narrower interests only in wages and working conditions. Books on metalworking have been available for centuries: one of the earliest printed books intended as a manual on metalwork was German metallurgist Georgius Agricola’s De Re Metallica, published in 1556. But with the advent of the internet, the wealth of teaching material and practical demonstrations has reached a critical mass. Now, it’s more possible than ever to teach oneself how to become a bladesmith without any formal training.
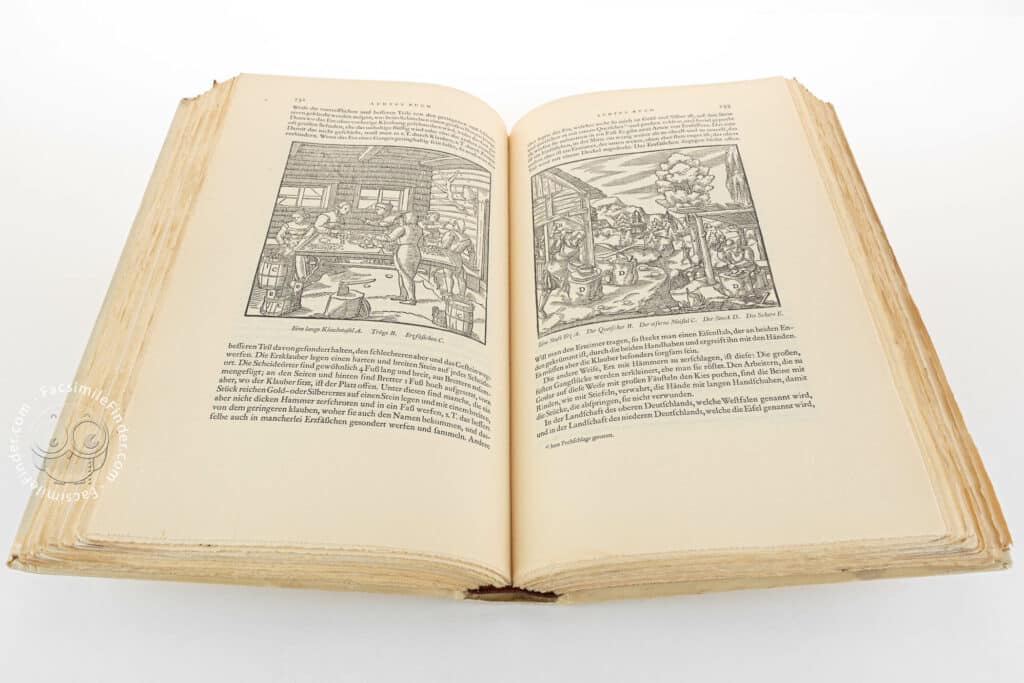
Many professional blacksmiths have uploaded excellent simple projects for starter blacksmiths. Black Bear Forge is a perennial favourite of ours – his demonstration of making a simple poker is a masterclass in straightforward blacksmithing technique. He’s thoughtfully separated out his more basic beginner videos into a separate YouTube channel. Other excellent places to start include Christ Centered Ironworks (who has almost 2000 videos uploaded at the time of publication!), and Alec Steele who has more than two million subscribers.
As well as digital media, there’s a wealth of blacksmithing and bladesmithing books out there. And there’s nothing like a physical book to consult when you’re in the forge – smearing your sooty fingers all over your mobile phone trying to squint at videos is all well and good, but a book is always easier! For a comprehensive list of book recommendations, see our article on The Best Bladesmithing Books.
Arguably, teaching yourself blacksmithing is the fastest way to get to a level of proficiency where you can begin making blades. It’s certainly the cheapest: blacksmithing books are rarely expensive, and there is a dizzying quantity of educational material available for free online. But, if you’ve ever learned in a context with others, you’ll find you develop better overall technique and to correct baked-in mistakes much moreso in a more formal learning environment. That said, everyone learns differently! DIY teaching is probably the way to go if you want to do bladesmithing as a hobby.
The Professional Route: Qualifications and Apprenticeships
Many traditional blacksmiths would tell you that the real way to get into making fine objects with historical metalwork is to undertake some kind of formal training. Modern blacksmithing training courses generally take two forms: apprenticeships, and qualifications, and either are great ways that will give you the skills you need for how to become a bladesmith.
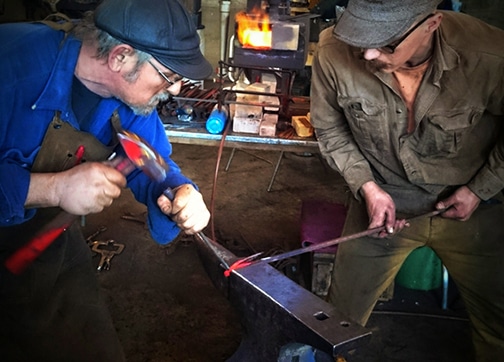
Apprenticeships are the much more traditional form of craft education. Historically, this would have taken the form of an agreement between the apprentice, usually a youth of only 11 or 12, and the master. The apprentice would work for the master for a long period of time – typically seven years – and the master would provide them food and lodging in return. This is known as an ‘indenture’, named after the wavy ‘indented’ cut made between the two halves of the signed apprenticeship contract, which fit one another uniquely as a proof of the agreement. Whilst this obviously looks to us like exploitative child labour (which it undoubtedly was), when the apprentice had finished their indentured period they would have acquired all of the skills required to set themselves up as a ‘journeyman’, who was then expected to leave the master’s town and travel from place to place practising their trade and honing their craft.
Fortunately these days, we no longer have restrictive trade guilds to enforce these archaic practises. Instead, apprenticeships are sometimes administered by the government as part of the education system (as in the UK), by an independent regulatory body (as with the Compagnons du Devoir in France), or by individual industries (as in the USA). Within traditional metalwork, individual blacksmiths will often take on one or two apprentices at a time – in the UK (where I’m most familiar with!), this will often be combined with ‘day release’, where the apprentice will spend one or two days per week at an educational institution.
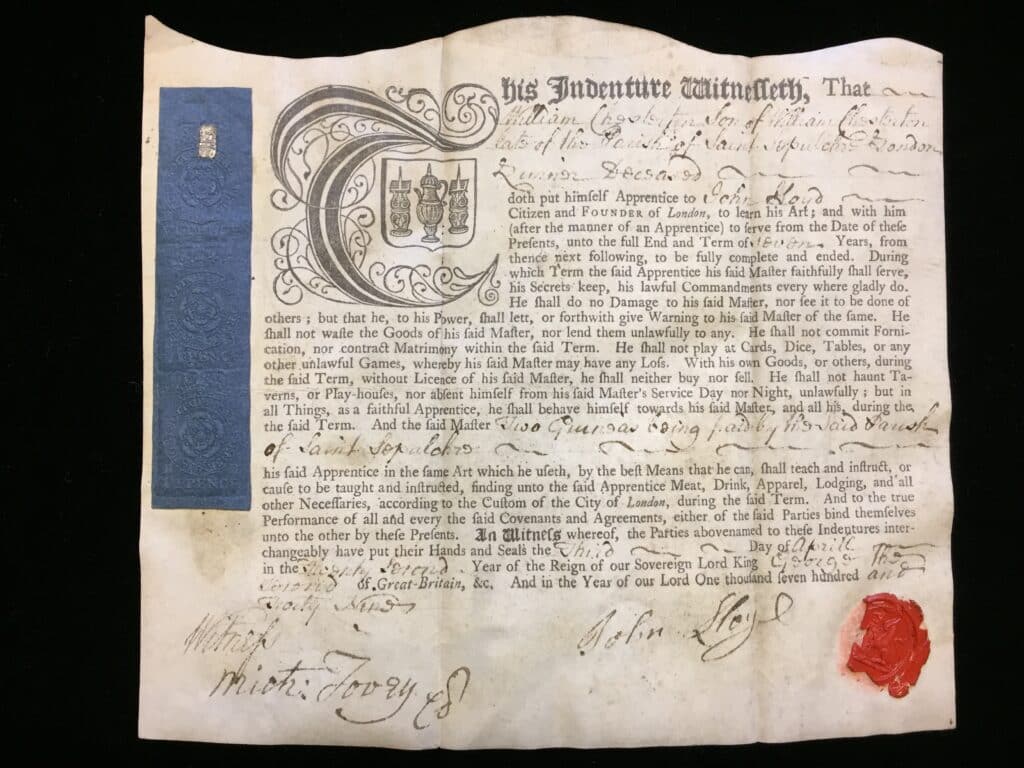
The other formal route into a career as a blacksmith is through a formal education setting. Many universities and colleges have begun to offer Metalworking & Design courses: the most famous in the UK is the National School of Blacksmithing at Hereford, which was founded in 1946, and now resides in a purpose-built center at the Center for Rural Crafts. It runs a wide range of BTEC (college-level) courses, and also runs a 3-year Bachelor of Arts (university-level) course in Artist Blacksmithing in tandem with Hereford College of Arts). Other colleges such as Myerscough College and SRUC (Scotland’s Rural College) also run accredited courses that are focused toward preparing students for a career in farriery or blacksmithing.
Again, as with self-directed DIY learning, there are both advantages and disadvantages to taking formal study in pursuit of bladesmithing work. A formal apprenticeship in a working forge would equip you with a solid grounding in a huge array of blacksmithing techniques – but it’s unlikely that you’d be working solely on bladesmithing. At the same time, apprenticeships usually last several years and are rarely well-paid – they’re generally only available to those who have a significant degree of social support (eg. school leavers or people who have savings). That said, if you’re seriously considering a career as a blacksmith, then formal qualifications, either through apprenticeship or a year-long college course would be a fantastic way to start. Shorter introductory courses are also much easier to fit around work or other commitments – some colleges even offer blacksmithing as a night course!
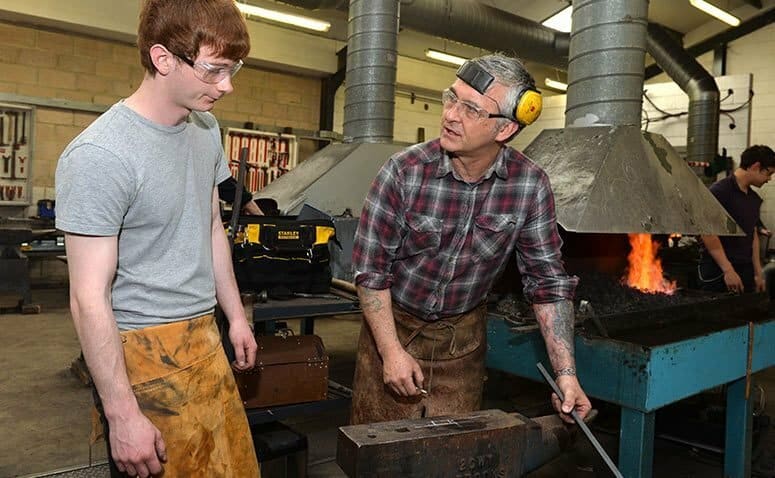
From Blacksmithing To Bladesmithing
So you may well have noticed that here we’ve been talking a lot about blacksmithing – but that’s definitely a subtly different thing to bladesmithing. I would go so far as to say that bladesmithing is a subset of blacksmithing, in contemporary usage: if a blacksmith is a general word for a metalworker who primarily uses a forge to apply heat to metals (predominantly various grades of steel), then a bladesmith is a blacksmith who primarily makes knives and other blades for survival, cooking and other uses. This sort of heirarchy doesn’t imply that a blacksmith is ‘better’ than a bladesmith; they are different specialisms who simply make different things. But it does perhaps imply that a general awareness of and proficiency in general blacksmithing is (if not a necessary prerequisite, then) certainly extremely useful to the bladesmith. A large proportion of blacksmithing is devoted to understanding the metals you work with: their characteristics, how they behave, their specific uses, and their pitfalls. This is all invaluable knowledge for a bladesmith – and you discard it at your peril!
So now you’ve learned how to start bladesmithing: take a taster day, see if you get the itch, and then choose between self-directed learning, or look at courses or apprenticeships in your area. As well, these aren’t mutually exclusive! Apprentice blacksmiths read lots of books on bladesmithing, and self-taught metalworkers can take short courses at any time. You’re master of your own path to mastery!
Tools of the Trade
In the Late Medieval or even Industrial past, blacksmiths were known as the ‘king of trades’, because they were the only profession who fabricated their own tools, and who made the tools for all the others. Toolmaking is a critical part of the bladesmith’s craft: you’ll need many tools that you just can’t buy at your local hardware store – and you’ll learn much more making (and breaking!) tools that you’ve fabricated yourself than you would just buying them off the shelf. In our next part on the profession of Bladesmithing, we’ll look at the tools and equipment you’ll need to start off – from tongs to forges to oxy torches! Until next time!